Sustainability in the Packaging Line
When it comes to packaging lines, many companies focus on meeting sustainability goals by finding a recyclable film for the package.
This is a great step and should be at the top of every list but make sure you do your due diligence before purchasing recyclable film in bulk and implementing it on the production floor.
Ask these questions:
- Will it run smoothly on the flow wrapper you currently have at the speeds you need to achieve?
- Does it meet your expectations for seal quality and product freshness?
- Is the package desirable to marketing and, more importantly, the consumer?
These are all things to consider and that is where we can help. Send us your film and product and we will test the quality, speed, and appearance for you to review at our in-house lab.
Recyclable film is not the only way to reach your Sustainability Development Goals (SDGs). Have you considered the efficiency of your equipment?
Eco-efficiency: Using fewer natural resources, water, and energy to greatly reduce the cost of production. When we think sustainability, we think of recycling, the environment, and ecosystems but efficiency is a vital strategy in meeting your SDGs (Sustainable Development Goals).
When we think sustainability, we think of recycling, the environment, and ecosystems but efficiency is a vital strategy in meeting your SDGs (Sustainable Development Goals). Investing in a packaging solution that creates more efficiency and less waste has become a crucial part of the success in satisfying consumer demands.
The Alpha 8 flow wrapper series is designed to do this.
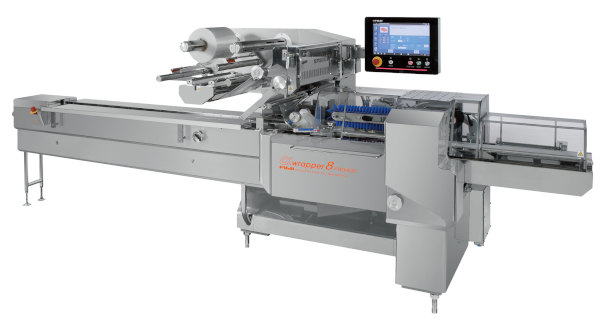
Key features for eco-efficiency:
Induction heat for sealing; Alpha 8 wrappers use 23% less energy than wrappers with standard brass mold heaters.
Shortened film route; reduces film loss in product change over and set run.
Easy to operate HMI; greatly reduces time spent operating and training to operate the equipment.
Maintenance Friendly; reducing maintenance and sanitation labor means less time using energy to perform important tasks. Features such as a tilt down center seal unit for easy maintenance and sanitary designed infeed conveyors that allow for tool free removal of belts for thorough, simple sanitation.
Additional eco-efficient features of the Alpha 8 wrapper series combined with the performance proven reliability of Formost Fuji equipment help companies meet their SDGs within their packaging lines.
Learning the eco-efficiency of your equipment. If your equipment is older or inefficient, this is a great place to start.
Inefficient packaging lines can cause higher energy usage, increasing your carbon footprint but how do you know if your equipment is running as efficiently as possible?
Compare your uptime vs your downtime. Tracking and understanding unplanned downtime is information you need to improve your productivity and effectiveness.
Make sure your wrapper speed matches the speed of the product being delivered to the infeed conveyor. If you wrapping at 100ppm but the product is being fed at 50ppm, this causes the wrapper to start/stop over and over which is hard on the equipment and very inefficient.
Check parts for wear and make sure a maintenance routine is established and reported. Is your air speed set at the appropriate PSI? Do you need pre-heaters for the film you are running?
The best way to check the eco-efficiency of your equipment is to schedule a “Machine Survey” with our service department. This is common practice and will help you determine if you are running your packaging equipment as efficiently as possible or if replacing your flow wrappers will provide you with long-term savings both financially and sustainably.
Click to Schedule a Machine Survey sales@abbeyequipment.com
Formost Fuji Ground Meat System – Flow Wrap Packaging for Case Ready Beef Products
Our hygienic ground meat flow wrap system is designed to provide the meat industry with a packaging option that is not only sustainable but also cost saving and eco-efficient.